电阻温升评估的相关测试总结
一.引言
我在《过零检测电路电阻过热整改分享》一文中遗留了两个问题,一是超过电阻额定功率使用,为什么不会快速损坏,二是实际功率不足额定功率的50%,为什么温升仍然很高?
本文通过理清电阻相关参数、结合实测数据进行分析,探索电阻温升的相关影响因素,解释额定功率对电阻散热的具体影响。
二.关键概念
1. 电阻额定功率
1)额定功率定义
电阻额定功率是指电阻器在特定环境温度下(通常为+70℃),可长期安全工作且不因过热导致性能劣化或永久损坏的最大功耗上限。
2)贴片电阻额定功率的测试标准
贴片电阻的额定功率是在以下条件下测量的
- 环境温度70℃
- 采用标准的FR-4玻璃纤维环氧树脂基板,板厚1.6mm
- 测试焊盘铜箔厚度需≥1OZ(35um),高功率测试场景推荐2OZ(70um)
- PCB铜箔面积:0805封装≥60mm2延伸铜箔(含焊盘),2512封装≥81mm2延伸铜箔(含焊盘)
2. 电阻降额曲线
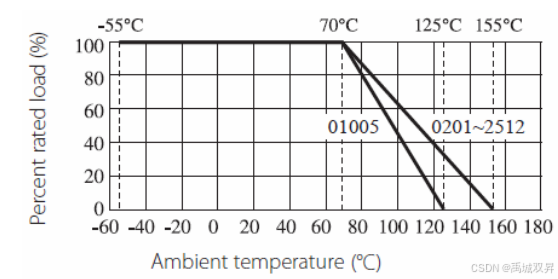
电阻降额曲线用于评估环境温度超过70℃时,在允许环境温度下,需要的降额标准。
如图1所示为电阻降额曲线,以0805封装0.5W的15K电阻为例,通过降额曲线,我们可以推算出热阻 ;假设我们允许最高环境温度为100℃,那么我们最大允许功率降至
;
3. 热阻
热阻是表示热量传递难易程度的数值。热阻值高意味着热量难以传递,反之意味着热量易于传递。
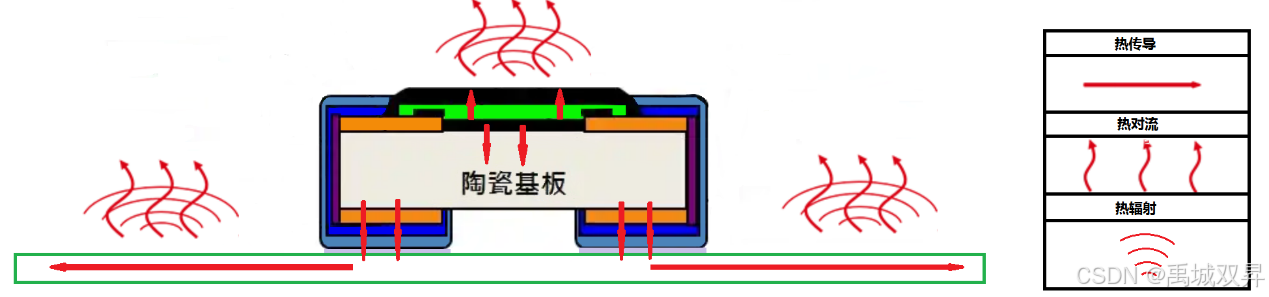
如图2所示,电阻散热有三种途径:热传导、热对流和热辐射。其热阻组成如下:
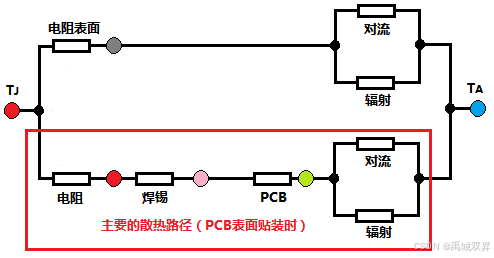
其中90%以上的热量通过PCB板的传导来进行【2】。在自然对流状态下,电阻表面通过热对流和热辐射对整体的散热贡献很小,可以先不分析。
电阻本体到焊盘的热阻θjp通常在15~50℃/W范围内。有人研究表明,当空洞率小于5%时,热阻增加很小,增幅小于1.06%;当空洞率达到20%时,热阻增加了6.53%;当空洞率达到79%,热阻增加了27.18%,详情请参考《功率器件无铅焊料焊接层可靠性研究》。根据IPC-A-610标准,要求BGA焊点空洞率≤25%,大功率器件接地焊盘通常要求≤10%。一些企业,像华为、联想等,空洞率要求更高。
焊盘到PCB的热阻影响因素较多,受铜箔面积、铜箔厚度、层叠结构以及散热过孔影响显著。有个经验数据,当铜皮面积≥12mm2时,热阻趋于稳定,约100℃/W。如果增加足够的散热过孔,可进一步降低到40~80℃/W(过孔可显著提升纵向导热效率)。
PCB板基材FR4导热性差,导热系数只有0.3W/(m.k),在自然对流以及铜箔面积不足的情况下,热阻范围150~300℃/W,强制风冷下,可降至50~100℃/W。通过扩展铜箔面积以及增加散热过孔,也可以降至20~40℃/W。
4. 温升曲线
大多数电阻厂商都不直接提供温升曲线,目前只找到KOA和VISHAY的规格书有温升曲线的信息。
如图4所示,为KOA的RK73H系列电阻的温升曲线,横轴表示的是实际功率和额定功率的比值,纵轴是温升数据,根据曲线,就可以查出实际功耗下对应的温升。
举个例子:假设选用的是W3A2系列电阻,其额定功率为2W,实际功率为1W,那么实际功率占额定功率1W/2W=50%,通过查询曲线,可以近似得出温升为130℃。
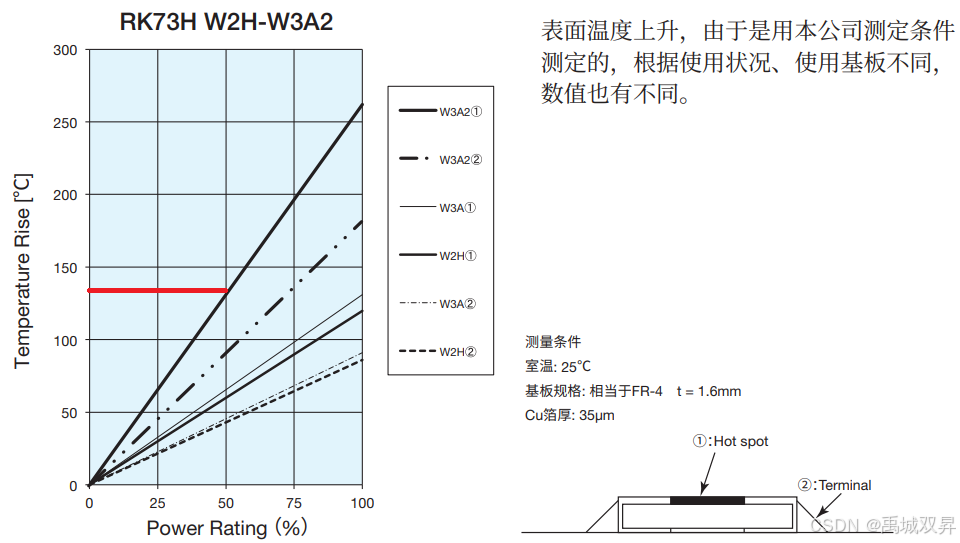
使用温升曲线来评估电阻温升,很方便,但需要注意厂家提供的温升曲线是在什么测试条件下得出的。比如KOA的RK73H系列电阻,明确指出的测量条件:室温25℃、基板为FR4,板厚1.6mm以及铜厚35um。如果不是同等测试条件,就不能直接照搬厂家的测试数据,但依然可以作为参考。
三.测试分析
将电阻焊接在PCB上,电压直接加在电阻两端,使用热成像仪进行测温。
以下测试数据都是在23~25℃环境温度下测得
1.数据记录
1)0805封装0.5W的15K电阻
电压 | 实际功耗 | 温升 | 热阻 |
20V | 0.0267W | 5.3℃ | 199℃/W |
32V | 0.0683W | 11.7℃ | 171℃/W |
43.3V | 0.125W | 21.2℃ | 170℃/W |
50V | 0.167W | 28.9℃ | 173℃/W |
60V | 0.24W | 41.9℃ | 174℃/W |
2)0805封装0.125W的8.2K电阻
电压 | 实际功耗 | 温升 | 热阻 |
20V | 0.0488W | 7.9℃ | 162℃/W |
32V | 0.125W | 20.2℃ | 162℃/W |
40V | 0.1951W | 32.7℃ | 167℃/W |
50V | 0.3049W | 51.6℃ | 169℃/W |
55.4V | 0.374W | 69℃ | 184℃/W |
60V | 0.439W | 81.7℃ | 186℃/W |
3)2512封装1W的5.6K电阻
电压 | 实际功耗 | 温升 | 热阻 |
20V | 0.0714W | 11.3℃ | 158℃/W |
30V | 0.161W | 24.6℃ | 153℃/W |
40V | 0.2857W | 43.2℃ | 151℃/W |
50V | 0.4464W | 65.2℃ | 146℃/W |
60V | 0.6428W | 91.6℃ | 142℃/W |
4)2512封装1W的8.2K电阻
电压 | 实际功耗 | 温升 | 热阻 |
20V | 0.0488W | 8.7℃ | 170℃/W |
32V | 0.125W | 18.5℃ | 148℃/W |
40V | 0.1951W | 28.1℃ | 144℃/W |
50V | 0.3049W | 44.1℃ | 144℃/W |
55.4V | 0.374W | 53.1℃ | 142℃/W |
60V | 0.439W | 61.6℃ | 140℃/W |
5)2512封装1W的15K电阻
电压 | 实际功耗 | 温升 | 热阻 |
20V | 0.0267W | 4.7℃ | 176℃/W |
32V | 0.0683W | 10.3℃ | 151℃/W |
43.3V | 0.125W | 18.7℃ | 150℃/W |
50V | 0.167W | 23.6℃ | 146℃/W |
60V | 0.24W | 35.2℃ | 146℃/W |
2.数据分析
1)电阻热阻随实际功耗的变化
如数据记录力红色字体标出的热阻数据,在电阻实际功率过小时,热阻会偏大。
这是因为电阻与环境温差太小,热量传递的驱动能力减弱,导致散热效率降低。从各电阻在不同电压下的测试结果来看,也呈现热阻随功耗增大而减小的趋势。
注意:超过额定功率使用,电阻热阻呈现不一样的特性。
另外,由于焊接空洞的存在,温差过小,焊锡未充分膨胀,空洞较大,也会造成低温时,电阻热阻偏大。
2)电阻热阻随封装尺寸的变化
电阻封装尺寸大,散热面积也也就大。因此,大封装尺寸的热阻要比小封装尺寸的热阻要小。比如上述数据中,2512封装电阻相比0805封装电阻的热阻,普遍大20℃/W左右。
3)电阻热阻随额定功率的变化
电阻热阻与额定功率并没有绝对的正相关关系。但通常电阻额定功率大,封装尺寸也大。
不过也存在封装尺寸一样,但额定功率不一样的。比如0805封装0.5W的15K电阻与0805封装0.125W的8.2K电阻,两者的实测数据显示,额定功率为0.5W的电阻热阻比0.125W的热阻还略大,当然这一点并不是客观规律,我推测,应该是焊接空洞的影响。由于没有检测焊接空洞的设备,缺少点说服力。但从已公开的论文资料来看,这样的推测也是合理的。
那么在不考虑封装尺寸影响的前提下,额定功率与热阻就无关吗?
当然是有关系的,当实际功耗超过额定功率时,额定功率大的电阻就显示出了优势。对比0805封装0.125W的8.2K电阻和2512封装1W的8.2K电阻的测试数据,就会发现,当实际功率超过额定功率时,电阻热阻会逐步增大。
四.结论
先来回顾开头的两个问题:
- 超过额定功率使用,为什么电阻不会很快烧毁?
- 电阻实际功耗不足额定功率一半,为什么温升仍然很高?
首先,从实测数据来看,超过额定功率使用,并不一定会快速损坏电阻;
其次,我们需要关注额定功率的测试条件——环境温度、板材、板厚、铜箔面积和厚度以及自然对流情况。如果我们的使用条件不一样,自然不能简单的对额定功率参数生搬硬套。说到底,电阻实际应用条件才是评估电阻温升的关键,但电阻的额定功率、功率降额曲线、温升曲线以及热阻,依然具有评估电阻散热的指导意义。
五.参考资料
1. 电阻温升评估利器:温升曲线
2. 隐藏的热陷阱:揭秘焊接空洞与温升的致命关联
3. 过零检测电路电阻过热整改分享
文章来源:电阻温升评估的相关测试总结